Production
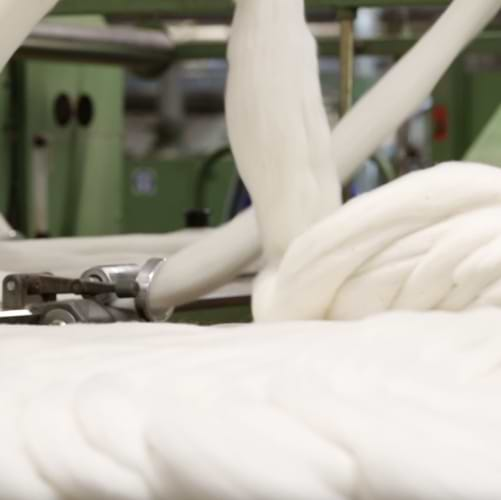
SPINNING
Our wool supplier Südwolle has its own spinning mills in Europe and China, where working conditions are closely monitored. The spinning is done as environmentally responsible as possible: all Südwolle yarns are Oeko-tex certified. This means that those yarns do not contain any harmful substances. The spinning mills reduce the water they use by filtering and reusing the waste water. This is an important tool in the sustainability process, and more so every year.
DYEING
The most sustainable, bluesign certified, recipes are used for dyeing. The use of fewer chemicals is one of the reasons that Joe’s pullovers do not or hardly pill.
And while we’re on the subject of dyeing and sustainability, we have to mention our Undyed-collection. A collection that doesn’t contain a single drop of dye. The colours are made by mixing the pure wool of white and brown sheep. It doesn’t come any more natural than that.
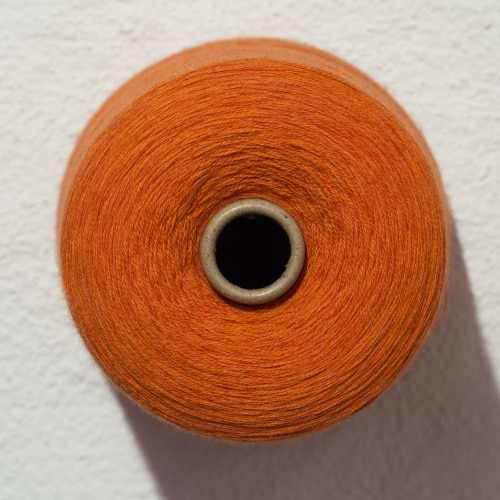
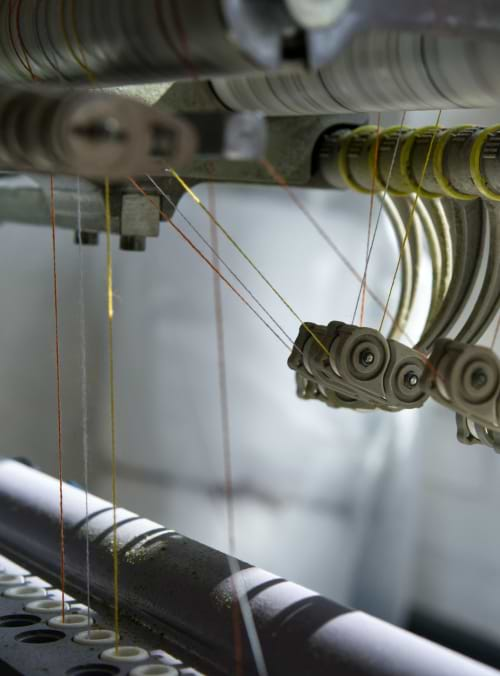
KNITTING
Some of Joe's cardigans and pullovers are made in Europe, but most are knitted in China. Not just because of the more favourable prices, but mostly because of the high quality and craftsmanship of our producers in China, who for decades have been known as fine knitting specialists. The bulk (80%) is made in a workshop in Shanghai. With wages around 20% higher than usual, the workshop has a loyal workforce. Working conditions in the factory are good. The workplace is well-lit. there is air conditioning, the toilets are clean and the workers get lunch every day. Every year they pass the SMETA, the leading audit worldwide on standards of labour, health and safety and environmental performance. To Joe this mean that the quality is guaranteed. Craftsmanship takes time and experience. It would make no sense to always hire and train new people. The same goes for the other workshop that makes Joe’s shirts (circular knit). Before Covid hit, we regularly made the rounds of the workshops. Now we go as often as we can. It’s how we harness mutual trust.
Joe’s pullovers are made on fully automated knitting machines. The sleeves and any collars are painstakingly hand-linked (with the exception of the Joe 3D-collection, which is made in one piece). The pullovers are then washed, with a minimum of softeners and chemicals, and dried on sticks in drying chambers. This slow method is more sustainable and the results are much nicer than if we would use machine-drying. Even better, the chances of pilling are reduced even further.